
Desktop Metal 3D Printers
BUILT-RITE TOOL & DIE
Overview
BUILT-RITE TOOL & DIE is a mold-making and design firm in Massachusetts with expertise in precision mold manufacturing. They specialize in the production of molds for plastic injection molding. These molds have complex designs, requiring extensive planning and precise execution.
The challenge
Small to mid-sized businesses like Built-Rite face increasing pressure from international and domestic competitors. Overseas manufacturers offer lower prices and domestic prototyping shops offer quick turnaround times for small quantities of parts. 3D-printing gives Built-Rite an opportunity to realize shorter lead times and reduced costs for quick-turn mold services when compared to domestic prototyping shops. The ability to iterate quickly is critical to winning project bids and for meeting tight deadlines.For Built-Rite, the Studio System™ introduces the ability to make quick-turn mold assembly components with a process that is far less labor-intensive than other equipment in their machine shop and more cost competitive than a third-party prototyping firm.
LUMENIUM LLC
Overview
LUMENIUM LLC IS A VIRGINIA-BASED COMPANY developing an innovative family of internal combustion engines.The Inverse Displacement Asymmetrical Rotational (IDAR) engine is a novel and totally singular design for producing powerful, efficient, internal combustion. Its unique geometry permits dramatic yet efficient work output from a small, light engine consuming less fuel and producing lower emissions.
The challenge
For Lumenium, the ability to iterate quickly has a direct impact on time-to-market and engine performance. Currently, they use an in-house CNC machine and wire electrical discharge machining (EDM) to make prototype parts, but the process is relatively time consuming and costly. Lumenium is seeking a faster, more costeffective approach to prototyping parts within the engine assembly. Parts within the IDAR engine must withstand the extreme heat and stress inherent to internal combustion engine operation. Each component must adhere to specific requirements—including high dimensional accuracy, strength under dynamic loads, and low thermal expansion. The weight of each part is an important consideration for overall power density and efficiency. Additive manufacturing allows Lumenium to meet these requirements and tackle complex part geometries—like internal cooling channels to improve engine performance. With the Studio System, Lumenium can bring this technology into their existing workspace for faster design iteration and functional prototyping.
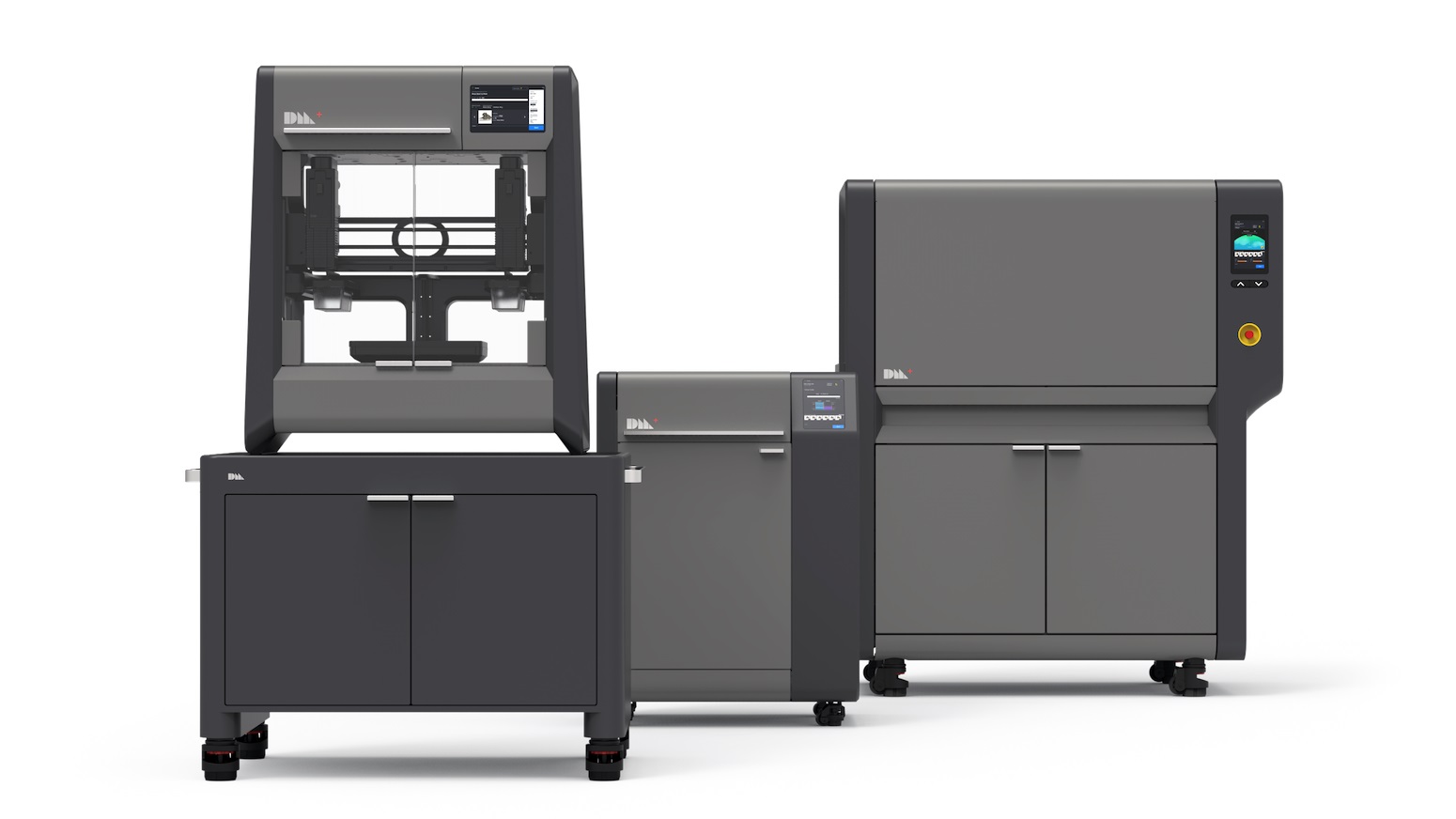